Mon - Sat : 9am to 7pm Sunday is CLOSED
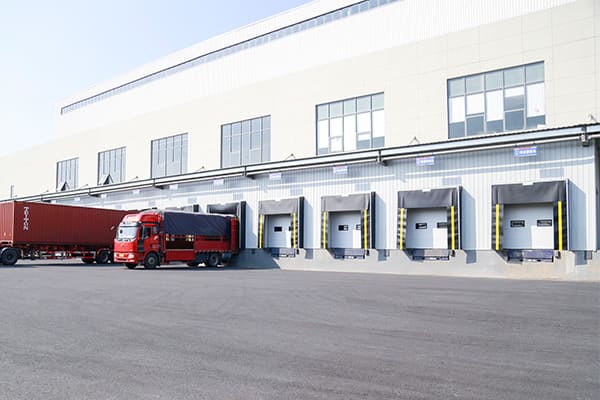
Introduction to Warehouse Loading Dock Desig
In modern warehouse logistics, loading docks play a crucial role. They serve as the bridge between the warehouse and external transportation vehicles, such as trucks and vans, and are the core areas for loading and unloading goods. Warehouse loading dock design refers to the configuration of platform dimensions, layout, equipment, and safety features to ensure efficient and secure movement of goods into and out of the warehouse. A well-designed loading dock not only speeds up logistics processes but also significantly improves operational efficiency and safety.
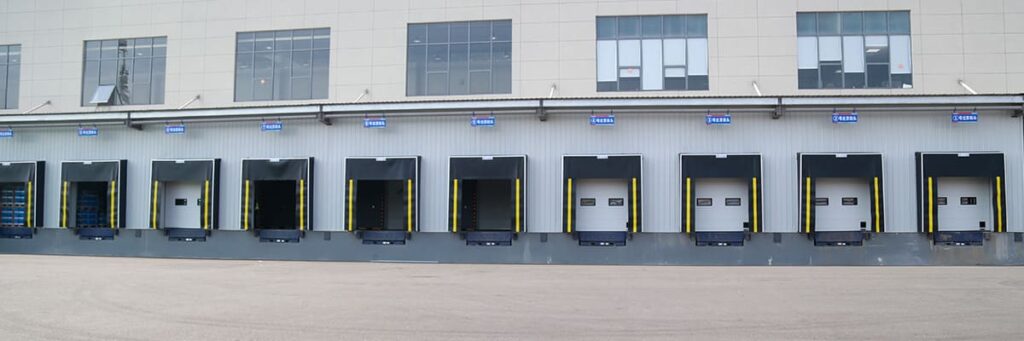
Why proper loading dock design matters for warehouse operations
Proper warehouse loading dock design is critical for enhancing warehouse efficiency. An optimized design helps reduce the time spent moving goods, minimize damage, and streamline the flow of goods in and out of the warehouse. A well-planned layout can reduce truck waiting times, eliminate operational bottlenecks, and maximize space utilization. For instance, the correct design of dock ramps ensures trucks can dock smoothly, reducing the complexity and time of loading and unloading, which ultimately boosts overall operational efficiency.
Common challenges in loading dock operations
Despite the crucial role of loading docks in warehouse management, many warehouses still face a range of challenges in actual operations.
- Unsmooth loading dock process: Long queues of trucks outside the yard, workers waiting for equipment or clear paths, these are typical signs of poor dock design.
- Accelerated wear of equipment: The dock leveler height does not match the truck compartment, or the equipment is used improperly, which will lead to premature damage to the loading dock leveler adjustment plate, vehicle restraints and forklifts, resulting in downtime and increased repair costs.
- Safety hazards: The loading dock is one of the most dangerous areas in a warehouse. Accidents can be caused by falling loads, improper handling, and so on.
ROI benefits of optimized loading dock design
Optimizing loading dock design leads to significant improvements in operational efficiency and cost savings. An optimized design minimizes goods damage, reduces manual intervention, and enhances material handling flow, all of which contribute to cost savings and increased profitability. Furthermore, a well-designed dock can extend the lifespan of equipment, reduce maintenance costs, and improve overall warehouse operations, resulting in long-term ROI for the business.
Essential Principles of Warehouse Loading Dock Design
A well-executed warehouse loading dock design is built on a foundation of essential principles that ensure safety, efficiency, scalability, and compliance. Understanding these fundamental elements is critical for any successful loading dock project.
Dimensional Requirements and Space Planning
Proper dimensional planning is at the core of every effective warehouse loading dock design. The dock height, width, and depth must accommodate the largest vehicles and material handling equipment used on-site. Sufficient maneuvering space for trucks, forklifts, and pallets is essential to avoid congestion and operational delays. Consideration of current and future throughput needs helps create a scalable design.
Traffic Flow Optimization
The flow of vehicles and personnel through the loading dock area significantly impacts warehouse productivity. Strategic placement of entry and exit points, clear signage, and unidirectional traffic routes minimize bottlenecks and collision risks. Efficient traffic management not only accelerates processes but also improves overall safety.
Safety Considerations and Compliance
Adhering to safety regulations and industry standards is non-negotiable in loading dock design. Anti-slip surfaces, guard rails, wheel chocks, and emergency stop mechanisms should be integrated to protect workers and goods. Compliance with local and international regulations — such as OSHA or EN standards — ensures legal operation and reduces liability risks.
Environmental Factors (Weather Protection, Lighting)
Environmental conditions can greatly affect loading dock operations. Canopies, dock shelters and seals, and proper drainage protect against rain, snow, and temperature extremes, ensuring year-round usability. Adequate lighting is vital for visibility and accident prevention, especially during night operations or in enclosed docks.
By following these fundamental design principles, warehouse loading dock design projects can achieve operational excellence, safety, and long-term value, meeting both current business needs and future growth.
Key Equipment and Components of Warehouse Loading Dock Design
Essential Loading Dock Equipment
A high-performance warehouse loading dock design relies on the integration of essential equipment and components that support efficient, safe, and flexible operations. Selecting the right tools for each aspect of the loading dock is crucial for productivity and risk management.
Loading Dock Levelers: Types, Features, and Selection Criteria
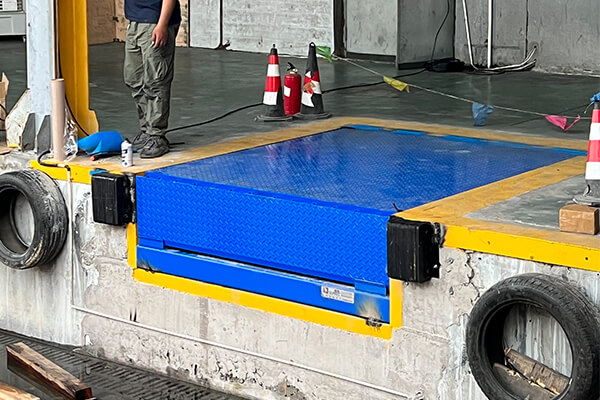
Loading Dock levelers bridge the height gap between the loading dock floor and the truck bed, ensuring smooth transfer of goods. There are several types, including mechanical, hydraulic, and other dock levelers. Selection should consider load weight, frequency of use, and compatibility with other equipment.
- Mechanical dock levelers are cost-effective and simple
- Hydraulic loading dock leveler models offer higher capacity and automation.
- Edge of dock leveler offers quick and easy loading and unloading with a low payload.
- Hydraulic dock lift: Raises and lowers loads through hydraulics for a wide range of load types and varying heights
- Vertical dock leveler: Saves space and adapts to more complex loading and unloading needs through vertical lifting capabilities.
Dock Seals and Shelter
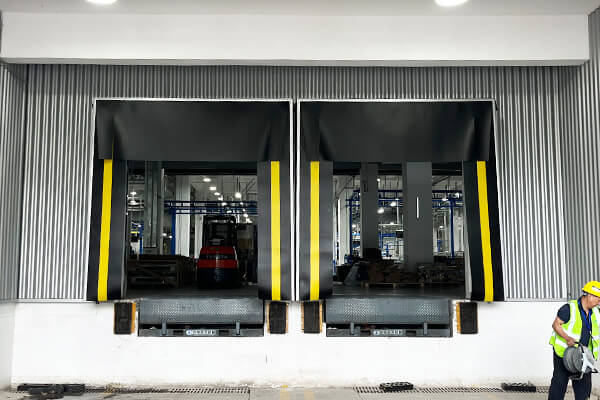
Dock seals and shelters provide a protective barrier between the warehouse and the vehicle. They prevent air, dust, and moisture infiltration, maintaining temperature control and product quality. Dock seals are generally used for tight fits, while shelters accommodate a wider variety of vehicle sizes. The right solution helps reduce energy loss and improves safety for warehouse staff.
Vehicle Restraint Systems
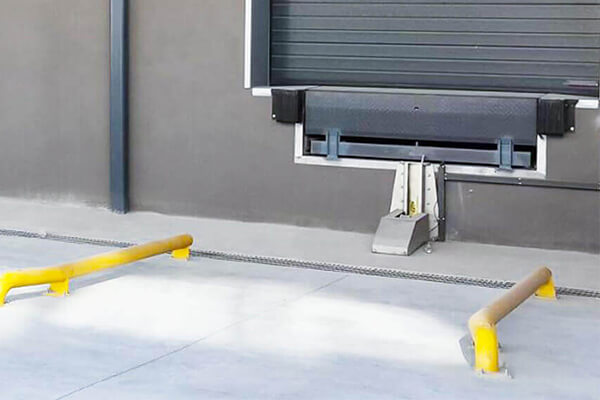
Vehicle restraint systems secure trucks in place during loading, preventing accidental movement that could cause injuries or product damage. Common types include wheel chocks, mechanical locks, and automatic restraint devices. Automated systems are becoming standard for high-volume docks due to their reliability and ease of use.
Lighting and Electrical Systems
Proper lighting is vital for safety and operational accuracy at the loading dock, especially in low-light conditions or at night. LED dock lights, motion sensors, and well-planned electrical outlets reduce accident risks and improve visibility. Energy-efficient lighting solutions also help reduce operational costs.
Safety Equipment and Warning Systems
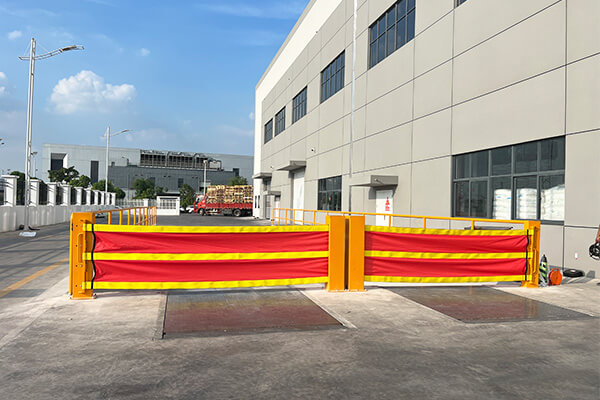
Dock safety features is paramount in every warehouse loading dock design. Essential safety equipment includes guard rails, safety barriers, dock bumpers, audible alarms, and visual warning signals. These systems alert personnel to hazards and prevent accidents, creating a safer working environment and supporting compliance with regulations.
Warehouse Dock Design Planning Process
Step-by-Step Design Planning
A systematic approach to warehouse loading dock design ensures that every detail is addressed for both current efficiency and future scalability. Careful planning at each step lays a solid foundation for operational excellence and long-term ROI.
Site Assessment and Requirements Analysis
The first step in any successful warehouse dock design is a thorough assessment of the site. This includes evaluating available space, vehicle types, traffic flow, and surrounding infrastructure. Detailed analysis of operational needs — such as expected throughput, types of goods handled, and safety requirements — guides the selection of dock type, equipment, and layout. Early identification of site constraints helps avoid costly modifications later.
Layout Planning and Dock Positioning
Strategic layout planning is vital for maximizing space utilization and ensuring smooth operations. The position and orientation of loading docks should facilitate efficient vehicle movement and minimize congestion. Proper spacing between docks, clear traffic lanes, and logical workflows all contribute to higher productivity. The integration of safety zones and signage is also essential at this stage.
Integration with Warehouse Operations
The loading dock design must seamlessly integrate with broader warehouse operations. This includes aligning dock locations with storage zones, picking areas, and internal logistics paths. Ensuring compatibility with material handling systems, such as conveyors or AGVs, further streamlines the movement of goods. Real-time communication between dock management and warehouse control systems improves visibility and coordination.
Future Expansion Considerations
A forward-looking warehouse loading dock design anticipates business growth and evolving logistics needs. Modular dock configurations, flexible equipment choices, and provision for additional dock positions allow for scalability without major disruptions. Planning utility connections, structural reinforcements, and technology upgrades in advance ensures the facility can adapt to changing demands over time.
By following a structured, step-by-step design planning process, any warehouse loading dock design project can achieve optimal results in efficiency, safety, and future adaptability.
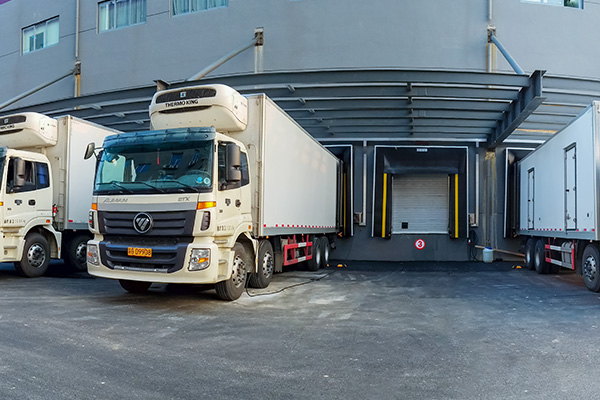
Equipment Selection Guide for Warehouse Dock
How to Choose the Right Loading Dock Equipment
Selecting the appropriate equipment is a critical step in warehouse loading dock design. The right choices directly impact operational efficiency, safety, and long-term costs. A systematic evaluation of needs, site conditions, and technical options helps ensure a robust and future-proof solution.
Factors to Consider When Selecting Dock Levelers
When choosing warehouse dock levelers, factors such as load capacity, frequency of use, vehicle types, and platform dimensions must be carefully considered. For warehouses with high turnover rates, heavy-duty hydraulic levelers are often preferable, while lighter operations may opt for mechanical models. The docking environment, climate, and compatibility with other equipment should also influence the final selection.
Comparing Hydraulic vs. Mechanical Systems
Hydraulic dock levelers offer superior automation, safety features, and load-bearing capacities. They are easier to operate, require less manual effort, and are suitable for continuous or heavy-duty use. Mechanical levelers are more cost-effective, simpler in structure, and suitable for facilities with lower usage or budget constraints. The choice depends on operational requirements, staffing, and long-term maintenance planning.
Cost-Benefit Analysis of Different Equipment Options
A thorough cost-benefit analysis evaluates not only the purchase price but also installation, energy consumption, operational efficiency, and potential downtime. While advanced hydraulic or automated solutions may require higher initial investment, their improved safety and productivity can yield substantial long-term savings. Mechanical options may offer lower upfront costs but could incur higher maintenance or replacement expenses over time.
Maintenance Requirements and Lifecycle Costs
Lifecycle costs are a vital consideration when selecting loading dock equipment. Hydraulic systems generally require less frequent maintenance but may involve higher repair costs if failures occur. Mechanical systems are easier to service but may need more regular attention. Establishing a preventive maintenance schedule and calculating expected lifespan and total cost of ownership helps warehouses make informed, cost-effective decisions.
By carefully evaluating all relevant factors, warehouses can select loading dock equipment that balances performance, safety, and cost, building a strong foundation for efficient and sustainable operations.
Common Issues and Dock Solutions
Despite careful warehouse loading dock design, operational issues can arise over time. Recognizing common problems and implementing effective solutions is crucial for maintaining efficiency, safety, and long-term performance.
Common Design Mistakes to Avoid
- Underestimating space requirements, which can lead to traffic congestion and inefficient workflows
- Inadequate dock height alignment with vehicle type
- Poor drainage planning
- Insufficient safety features (such as guardrails and warning systems)
Maintenance Issues and Preventive Measures
Neglecting regular maintenance is a major cause of equipment malfunction and downtime. Common issues include worn dock levelers, malfunctioning restraint systems, and inadequate lighting. Establishing a preventive maintenance schedule — including routine inspections, timely lubrication, and replacement of worn parts — can significantly extend equipment lifespan and reduce unexpected breakdowns.
Retrofitting Existing Loading Docks
Older loading docks may lack modern safety features or capacity for today’s operational demands. Retrofitting can include adding dock levelers, upgrading lighting, installing vehicle restraint systems, or improving insulation and weather protection. A careful assessment of current infrastructure and needs allows for targeted, cost-effective upgrades without complete reconstruction.